Understanding the Trick Components and Repair Service Methods for Packaging Machine Upkeep
Reliable maintenance of packaging makers hinges on a thorough understanding of their essential parts, consisting of the frame, drive system, and sealing mechanisms. Identifying usual maintenance problems, combined with the execution of preventative methods and repairing techniques, can considerably improve maker integrity.
Trick Components of Packaging Makers
Product packaging devices consist of numerous key components that collaborate to guarantee reliable and reliable product packaging procedures. At the core of these makers is the frame, which offers structural stability and houses the different operating parts. The drive system, typically a mix of equipments and motors, helps with the motion of parts, making it possible for specific procedure throughout the product packaging cycle.
One more vital element is the conveyor system, which carries products through various stages of the product packaging procedure. This is commonly enhanced by sensors and controls that keep track of the position and rate of things, making certain synchronization and lessening errors. The filling system is critical for accurately giving the ideal quantity of product into plans, whether in liquid, powder, or solid kind.
Sealing systems, consisting of warm sealers or glue applicators, play a crucial role in safeguarding bundles, stopping contamination and extending life span. In addition, labeling systems are indispensable for supplying required item details, making sure compliance with regulations. Finally, the control board, furnished with user-friendly interfaces, allows drivers to manage maker functions, screen efficiency, and make changes as needed, ensuring optimal efficiency and effectiveness in packaging operations.
Common Maintenance Concerns
Reliable operation of product packaging machines depends greatly on normal maintenance to stop usual issues that can interfere with production. Amongst these issues, mechanical deterioration is widespread, particularly in components like motors, seals, and conveyors, which can result in unforeseen downtimes. Additionally, imbalance of components can result in inefficient procedure, creating items to be inaccurately packaged or damaged during the process.
One more common maintenance problem includes the build-up of dust and debris, which can hinder the maker's sensors and relocating components. packaging machine repair service. This not only impacts performance however can likewise position security dangers. In addition, lubrication failings can bring about raised rubbing, causing getting too hot and ultimate part failing.
Electrical troubles, commonly originating from loose connections or worn-out electrical wiring, can disrupt equipment features, bring about substantial production hold-ups. Software application problems due to incorrect setups or out-of-date programs can impede the maker's operation, necessitating instant treatment. Dealing with these typical upkeep problems proactively is essential for making certain optimal performance and long life of product packaging equipment.
Preventative Upkeep Strategies
Executing preventative maintenance techniques is critical for maintaining the efficiency and integrity of packaging equipments. These strategies incorporate a systematic technique to maintenance, concentrating on the regular examination and servicing of equipment to preempt possible failures. By adhering to a set up upkeep program, drivers can identify deterioration on parts before they cause substantial break downs.
Trick elements of a preventative maintenance method include routine inspections, lubrication, component, and cleansing substitutes based on producer referrals. Utilizing lists can improve this process, making sure that no vital tasks are ignored. Additionally, keeping accurate records of upkeep tasks help in tracking the maker's performance over time, helping with informed decision-making relating to future upkeep needs.
Educating team on the significance of preventative maintenance enhances compliance and cultivates a society of positive care. Carrying out a predictive upkeep element, using data analytics and sensor modern technology, can better enhance equipment efficiency by predicting failings before they occur.
Troubleshooting Strategies
When confronted why not check here with breakdowns or inefficiencies in product packaging equipments, employing methodical troubleshooting strategies is essential for recognizing and dealing with issues swiftly. The primary step in effective troubleshooting is to develop a clear understanding of the device's operational specifications and performance metrics. This entails evaluating the machine's specs, as well as any kind of error codes or alerts shown.
Following, operators need to Discover More Here perform a visual inspection, looking for noticeable signs of wear, imbalance, or damage. This often consists of examining belts, sensors, and gears to determine prospective sources of breakdown. Gathering functional information, such as production prices and downtime logs, can likewise offer understandings into persisting issues.
When potential issues are recognized, making use of a rational approach to isolate the source is essential. This might need screening private parts or systems in a controlled way. Engaging in conversations with operators who interact with the machinery on a regular basis can yield important responses about unusual behaviors or patterns.
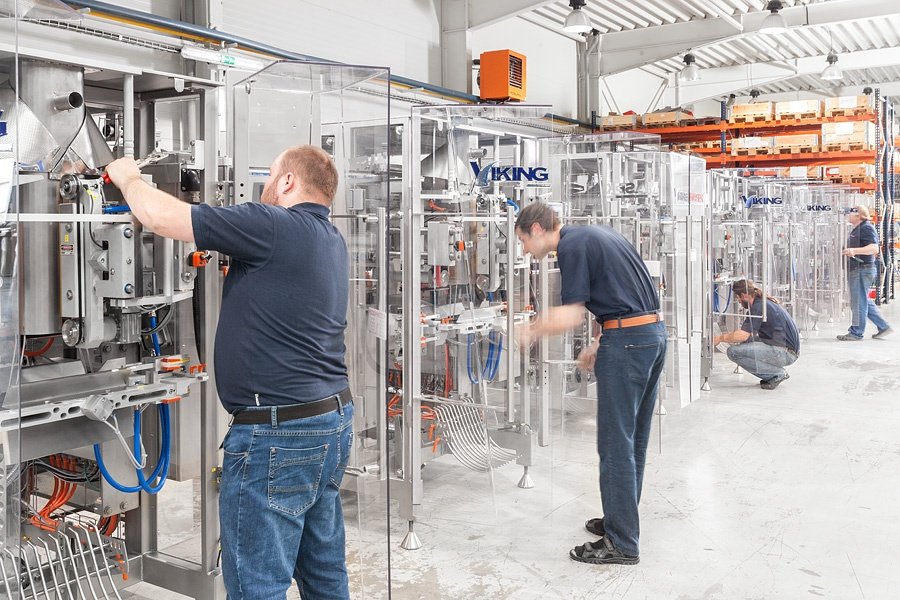
Fixing and Replacement Ideal Practices
A detailed understanding of repair and substitute best methods is essential for preserving the long life and effectiveness of product packaging machines. Consistently assessing the condition of equipment elements permits timely treatment, stopping more substantial concerns that can cause costly downtimes.
When repairs are essential, it is necessary to utilize OEM (Original Devices Manufacturer) components to guarantee compatibility and efficiency. This not only protects the integrity of the maker but likewise upholds guarantee arrangements. Furthermore, it is recommended to keep a stock of look at these guys crucial extra components to help with fast replacements and reduce operational disturbances.
For intricate repair services, engaging certified specialists with specialized training in packaging machinery is recommended. They possess the know-how to identify concerns properly and carry out repair services effectively. Moreover, recording all repair service activities and parts replacements is critical for maintaining a comprehensive maintenance background, which can help in future troubleshooting.
Last but not least, carrying out a positive method, consisting of normal inspections and predictive upkeep strategies, enhances the dependability of product packaging machines. By adhering to these ideal techniques, businesses can guarantee ideal equipment performance, decrease functional risks, and prolong devices life-span.
Conclusion
In conclusion, a thorough understanding of packaging maker parts and reliable maintenance methods is vital for ideal performance. By carrying out these techniques, organizations can ensure the longevity and efficiency of product packaging equipments, ultimately contributing to improved operational productivity and decreased expenses (packaging machine repair service).
Reliable upkeep of product packaging machines hinges on a comprehensive understanding of their crucial parts, including the frame, drive system, and securing devices.Reliable procedure of packaging devices relies heavily on normal maintenance to prevent common issues that can disrupt production.Carrying out preventative maintenance techniques is crucial for maintaining the efficiency and integrity of packaging machines. Additionally, maintaining accurate documents of upkeep tasks aids in tracking the machine's efficiency over time, facilitating educated decision-making relating to future maintenance needs.
